When fluid flows through a plain tube, the portion closer to the wall is subject to frictional drag, which slows down the fluid at the wall. This laminar boundary layer can significantly reduce the tube side heat transfer coefficient and consequently the performance of the heat exchanger.
By using wire turbulators in the tubes the laminar boundary layer will be disrupted, creating additional fluid shear and mixing, thereby minimizing the effects of frictional drag.
Turbulators are particularly effective at enhancing heat transfer efficiency in a plain tube design operating at low Reynolds Numbers (laminar to transitional flow). Although the heat transfer increase is greatest in the laminar flow region, significant benefits can be obtained in the transitional and turbulent flow regimes.
The turbulators offered by sabafarin co. are manufactured from wire in the form of a looped spiral as illustrated below.
Wire turbulators have many advantages over Fin or Spiral sheet metal types.
The density of the turbulator can be varied to suit the liquid or gas flowing through the tube to give maximum excitement and heat transfer coefficient with a minimum loss of pressure thus economizing on the length, diameter or number of tubes required per unit and allowing flow pumps to be kept at a minimum size.
Our turbulators are normally manufactured with a small eye at one end (to facilitate easy pull through the tubes) and a tail can be left at the other end for adjusting to any follow up length, when tubes over 3.00 metres long are involved.
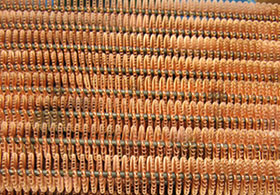
Rectangular-Plate Turbulators:
Twisted style turbulators with unlimited length and sizes can be used in any application . Turbulators are inserted into heat exchanger tubing to increase the flow through a tube, effectively increasing heat exchanger rates and abilities.
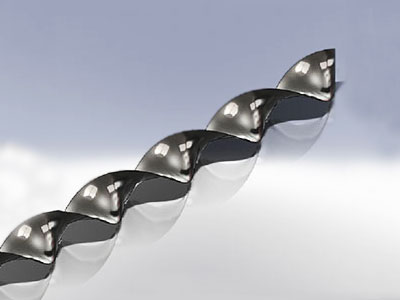
Star Section turbulators:
These turbulators are utilized for manufacturing air cooled oil coolers and compressed air after coolers.